In this issue:
Missed the last issue? You can read it in full here…
MTA’s Terry’s tribute
A lot of professional cleaners come into the cleaning business and for all kinds of reasons.
Setting up MTA Carpet Cleaning helped owner Terry Aldridge through personal grief.
“My wife Mandy passed in 2016,” he tells us. “I was driving HGVs at the time but before that had worked as a cleaner for seven years. When her dad suggested I help manage my loss by doing something different for work, I decided to go back to an occupation I loved.”
And Terry’s doing it for someone he loved. “MTA stands for Mandy Terry Aldridge, our branding is yellow, Mandy’s favourite colour, and the logo is an owl, her favourite animal,” he explains.
He set the business up in 2017 and ‘went Prochem’ from the off and today runs a Steempro Powermax and most recently an additional Steempro Powerplus.
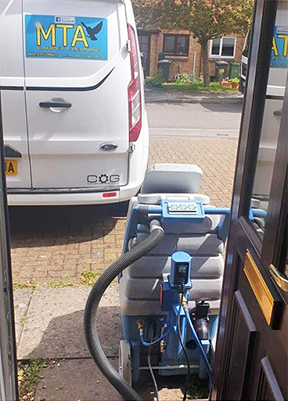
Terry’s tech
“I love them,” says Terry. “They do a fantastic job and I have had terrific support from Prochem’s distributor Cleaning Solutions in Taunton.”
Taunton is hardly local to Berkshire but Terry pushes the logistics one side.
“I’m used to long-distance driving,” he says, “and anyway, if you get good service, it’s worth putting in a few more hours yourself.”
Didcot-based Terry works domestic and commercial contracts within an hour’s drive from home.
“It basically takes me into Wiltshire, Oxfordshire and Buckinghamshire as well as my home county”, he says.
Most of his work is domestic and comes from recommendations via social media posts of videos and before and after photos. “I also do end-of-tenancy cleans and a bingo hall in town,” he says.
“My wife and I used to go there weekly and when they heard I had taken up cleaning again, they asked me to do their premises, which was very kind. So, I carry out a deep clean of the entire building’s carpets every six months.
A Prochem fan, Terry also uses the company’s chemicals. Favourites include S775 Extraction Plus, S760 Liquid Defoamer, S710 Trafficlean, B224 Cherry Carpet Deodoriser and B117 Lemon Refresh (“I need bigger containers of that one,” he exclaims. “I get through a litre a week!”)
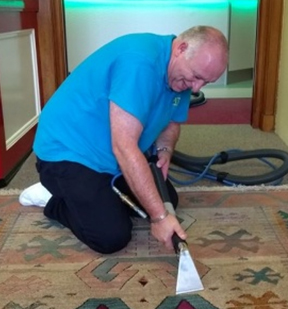
Terry cleans up at the Bingo
Looking to the next decade, Terry has his sights set on getting more commercial business and upgrading to a Prochem truckmount machine.
He’ll be back at Cleaning Solutions, of course, where the company’s Will Smyth plans further diversity for this distribution business next year including launching a new lease purchase plan.
“Terry could be interested in this,” he says. “Leasing seems more beneficial than outright purchase for some of our customers not least as it removes the need for capital outlay, enabling the machine to pay for itself as you go along.
“Right now, we’re doing a deal where you pay nothing for the first six months!”
Always read the label
Charting the evolution of Prochem chemical labelling reveals some striking changes. Parag Patel, Chemical Product Manager, explains why it’s more about your safety than our image …
Labelling text and – particularly – safety information provided has changed enormously over the years.
Take Extraction Pro: back in the 1970s when this was first produced (as S774 Thermo Pro) it came with the characteristic original Prochem “happy man” logo printed on a paper label. Looking at the evolution of the label over the years the label has changed drastically.
In 2010, the name changed once more, to Extraction Plus and the product was reformulated to improve performance.
More recently, we changed the label to wrap around half the bottle. This enabled Prochem to keep up with the new label regulations requirement and make the label look less congested with all the information.
It still retains the very latest labelling design on chemical resistant laminated plastic complete with the Prochem logo, user symbols, QR code and bar code – many elements absent from the original labelling when the product was first launched.
Extraction Pro to 2010’s Plus – labeling innovation at Prochem …
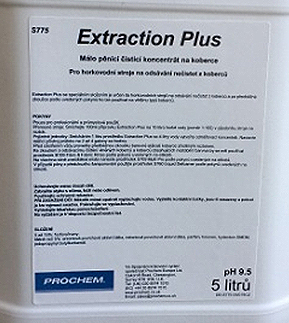
Extraction Plus – in Czech
Today’s packaging incorporates the latest composition, risk and safety phrases. With the addition of the QR code, customers are able to access the safety data sheets more easily and on the move. In the 1970s, the standard precautionary message was “Keep away from children and animals”, if the product was not classified under the old CPL system.
Prochem has worked to ensure that its packaging and product information goes that extra mile beyond required standards. Label information is backed up by each product’s specification data sheets and by the same information online.
And the ‘message’ is spreading.
Now the company also produces secondary labels for products which are exported in many more different languages than before including Czech, Latvian and Portuguese as well as the previous Polish, German, Dutch, Hebrew, etc.
Prochem Europe Safety Data Sheets are available from your local supplier or for the most up-to-date version, simply download or access instantly from www.prochem.co.uk
Cleaner – stay safe
Do you know what your liabilities are to current Health & Safety laws and good practice? asks Prochem Europe trainer Adam Jankowski …
Too many businesses discover too late about the need for compliance to legislation. On Prochem training courses we regularly get asked about legislation and the dos and don’ts surrounding the cleaning industry.
So, here are some Practical Tips to ensure that you and your employees comply with the latest requirements of health, safety and environmental law:
Keep up to date copies of safety data sheets (SDS) for each chemical product used in your operation.
Originals should be kept in an office file and copies in each vehicle in which the chemicals are transported and/or stored. Hard copies are the most reliable, as electronic devices rely on battery power. The most up-to-date versions will always be available on our website at www.prochem.co.uk
Produce a brief assessment in writing for each chemical product used and the safety procedures for handling and storage of each product.
Highlight on each assessment the personal protective equipment required (gloves, safety glasses etc.) and get a signed copy of the complete assessment from your employee(s) confirming that they have read and understand the safety requirements. Refer to HSE guidance on how to carry out a COSHH Risk Assessment.
Issue any personal protective safety equipment (PPE) required by the assessment to each employee.
Once again, get a signed receipt to confirm that this has been received by the employee. Remember that it is the employer’s legal duty to provide all the necessary PPE to an employee. The employer bears the cost of PPE, not an employee.
Always dispose of waste cleaning solution (water-based) to a toilet or customer’s/utility sink connected to a waste water sewage system.
Never dispose of waste water to a roadside drain or hand wash basin or kitchen sink.
Any solvent-based cleaning residues should be stored in appropriate containers (see SDS).
These should be marked with the solvent manufacturers’ original product label and the words “Hazardous Solvent Waste”, taken to the nearest waste recycling facility and handed in at the appropriate area for paints and solvent wastes. You will have to pay for their disposal, as it is waste produced in a commercial process.
Always allow plenty of ventilation when cleaning and spraying.
That way you ensure the quick dispersal of any vapours or spray droplets and to speed up the drying process.
Ensure that all persons not involved in the cleaning process are kept out of the area where cleaning is taking place.
And for as long as possible after cleaning too, allowing adequate ventilation and drying before the area is re-occupied.
Consider the ‘good practice’ of providing a Duty of Care leaflet*.
Never leave cleaning product containers unsecured in vehicles.
Nor for that matter unsupervised in households, particularly where young children are present.
Is your electrical cleaning equipment requiring service or repair?
Insist that you are provided with a test sheet or certificate of electrical safety which states that the appliance has been tested and passed the requirements of Portable Appliance Testing (PAT) in compliance with The Electricity at Work Regulations. Keep a copy of this certificate or test sheet both at your office and in each vehicle that is used to transport the equipment. Remember, a PAT Test is only valid for the time it is carried out and should be renewed regularly, subject to risk assessment and according to your company’s policy, as well as after any repair to the machine.
Use the correct technique for lifting heavy equipment.
Ensure that any employee is shown the correct technique and that he/she signs a statement to the effect that he/she understands the risks of injury from lifting heavy objects incorrectly. The correct technique is to keep a straight back and bend the knees to achieve a straight back posture and keep the weight near to your body whilst lifting. Manual Handling and Lifting guidance is available from HSE.
Attend a health and safety course
All HSE publications are available for free if downloaded from their website in pdf format. Printed books need to be paid for.
Too many businesses discover too late about the need for compliance to legislation. Don’t let your customer be the one to tell you.
Further information from the Health & Safety Executive at www.hse.gov.uk and from www.ncca.co.uk
*A Duty of Care leaflet is a written document that explains to your customer how to care for the items after they have just been cleaned, for example, to take care when walking from the dampness of the carpet onto a hard floor, as damp soles of footwear could cause you to slip.
(Adam Jankowski, Tech IOSH, is a Director of The Restoration Academy UK Limited and regular Prochem trainer)
Nick takes off with Prochem
Business is literally taking off for Nick Woods at Herts & Essex Carpet Cleaning.
If he’s not on site at Stansted Airport or the US military airbase at Mildenhall, he’s up in the clouds over London on the 46th floor of the city’s iconic Leadenhall ‘Cheesegrater’ building.
All this buzzing about necessitated upgrading vans and Nick’s just taken delivery of a new Ford Transit.
With his Prochem Sapphire SS370 truckmounted extractor now installed, this has been something of a game-changer for Nick. “I pitch for the best price I can get and that means looking the part and having the technology to back that up,” he says.
“The Sapphire is a fantastic machine – I love it. It’s been so well thought through.
“It runs hot, fast and very smoothly – just smashes through the work. And it only takes three to four hours before a job is dry and ready to use.”
This is Nick’s fifth year in the cleaning business since he was made redundant from his job as a regional sales manager. “It seemed to me the moment for a change of career and I’ve no regrets,” he says.
Based in Dunmow, Herts & Essex enjoys strong levels of domestic work, too. 2020 is a target year for Nick to add more commercial sites to his portfolio. Wife Ellen is coming on board with the business to help out and work is expanding to take in stone floors and upholstery cleaning.
“Prochem have been a huge help to us not least in supplying some great solutions for this machine,” he says. “Ultrapac Renovate, Citrus Gel and Urine Neutraliser particularly get the thumbs up.”
Nick’s en route to bigger things and the Sapphire is the jewel in his crown.
Carpet – good for the health
There is constant discussion within the care industry as to whether carpets or hard flooring are more suitable to use.
Hard flooring is usually deemed to be more hygienic – in fact, given the nature of application, you could argue that the fight is over before it started.
That said, take out the carpet and the care home loses something of its lustre: those values of quality and comfort (and for that matter, improved acoustic performance) that managers strive to ensure for their residents’ comfort.
Yet both hard flooring and carpet have their place, not least because today’s floor care technology offers credible solutions for each.
So let’s big it up for carpet even if, yes, it takes a beating in care homes. From a high volume of footfall to the constant use of wheelchairs and hoists, not to mention the spills that impact on performance, carpet in care homes and hospitals needs to be maintained (if not deep cleaned) regularly.
Coffee and tea spills, trod-in food, sugars and oils within medicines, high-fat protein drinks, drops of oil from hoists and wheelchairs, as well as all other bodily fluids are the most common encountered in healthcare interiors.
Probably too many cleaners believe that carpet cleaning is all about the machine with perhaps too little thought given to what’s put in it.
And they race around leaving little time from when the detergent is sprayed down to when the machine extracts the moisture back: often not enough time for the cleaning detergent to release those tough spills.
As ever, some pre-planning makes the job easier. If the machine does not simply flush-out the spill, whatever it is, then it may benefit from some pre-treatment.
Two useful problem solvers are Prochem’s B144 Stain Pro and E840 Citrus Gel.
The former is a “protein-breaker” that is simply lightly sprayed onto the spills, left for two to five minutes, and then rinsed with the extraction machine or even blotted back with white absorbent paper roll.
It helps release the protein found in food, drink, blood, vomit and faeces from the carpet and makes it far easier to remove.
Citrus Gel does exactly the same but focuses on oil and sugar based spills; and being a citrus-based gel, it simply dissolves the oils and sugars before being rinsed or blotted away.
Another common problem is over-dispensing solution. A little can go a long way with contemporary chemicals.
There is a misapprehension that if a carpet is cleaned too often, it can become sticky and get dirtier quicker. This, however, is often caused by the over-use of detergent in the machine.
Always use the amount designated on the manufacturer’s label, by diluting correctly and do not simply glug the product into the machine and the carpet will be kept to a high level of appearance for longer and improve cost efficiencies in the process.
Of course, it is not always over-use of chemical. Using an unsuitable chemical, such as a high-alkali or hard surface detergent can exacerbate matters too, by leaving a residue on the fibres that once dried, can cause re-soiling.
In most care environments a specifically formulated acidic detergent in the machine is more suited to ensure that the carpet is left ‘rinsed’ and residue free.
Prochem has been supporting the care industry since its inception in 1974 with a wide range of task-specific solutions and systems to tackle carpet care.
A mainstay of the product range is B112 Neutra-Soft®. It’s been exclusively designed for this market and can be used firstly as an extraction cleaner via a carpet extraction machine; a urine contamination pre-treatment for neutralising those inevitable leaks, spills and malodours; a fresh deodoriser to please the nose; and finally, as a rinse agent to leave minimal residue.
The ultimate all-in-one solution, it makes life so much easier for the machine operative by removing the need for a carpet detergent, deodoriser and urine contamination treatment.
And the 11.3 litre capacity, Prochem Fivestar carpet extraction machine is ideal for care home use: it’s quiet and easy to manoeuvre and a 5 litre concentrate bottle of Neutra-Soft will provide up to 44 complete machine fills – that equates to just over 2p per litre in cleaning solution cost.
Prochem provides on-site product training and demonstrations to large care home groups, independent homes and private hospitals, and supplies products to healthcare environments across the country via its extensive distributor network.
Find out more about odour control and carpet cleaning in healthcare and more at prochem.co.uk/cleaning-technical-help-guides
Reaching for the Sky
A little ‘movie magic’ is getting business moving along nicely at one London carpet cleaning business that’s clearly ‘reaching for the sky’.
In just eight years, Wimbledon-based Sky Cleaning Ltd has carved itself a niche not only within its locality in the south west quadrant of the city but across the capital and out to the M25 motorway.
That’s when Bulgaria-born Stan Kanchev came to the UK with a mind to start a new career. Hard work, the right tools, and effective marketing have paid dividends for he and his 10-strong team of cleaners.
“London presents many challenges for service companies but if you put the hours in and stay professional, you can thrive here,” says Stan.
He recognises the benefits of being based in an affluent part of town but the competition is correspondingly high. That’s why Sky Cleaning uses Prochem Europe machines and chemicals.
“We run two Prochem Steempro Powermax extraction machines. The Heat ‘N’ Run functionality is terrific and they are perfect for the job,” says Stan.
“The Prochem brand represents quality and that’s an ethic we share as a business. We love the company’s solutions, too. Power Burst and Prespray Gold are two favourites that spring to mind.”
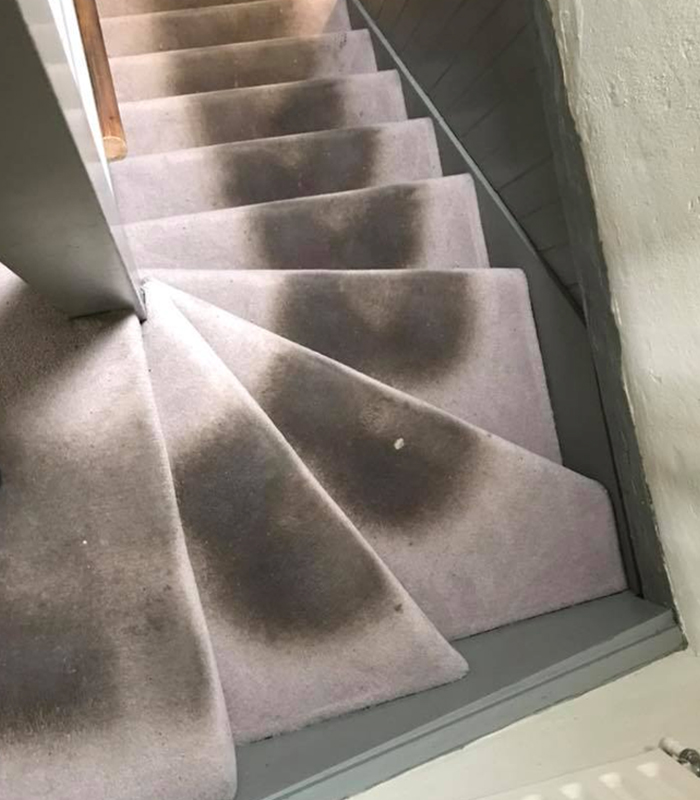
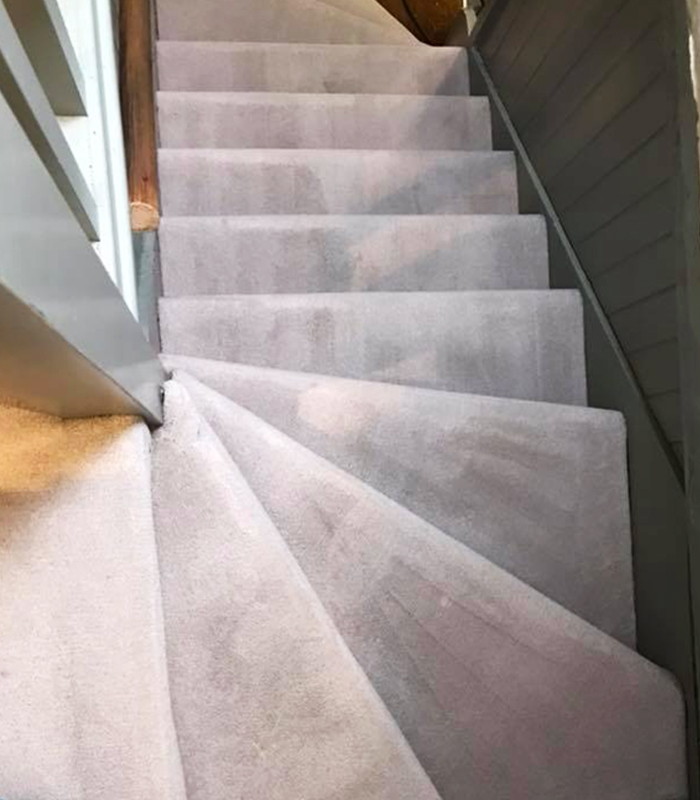
A Sky Cleaning customer’s stair carpet – before and after a Powermax clean …
Stan buys his solutions from Prochem distributor Forestdale Business Services, based in Mitcham. “I get a good service from Forestdale so we keep going back,” he says.
Evidence of Sky’s commitment to Prochem products can be found the moment you land on its website home page. Sit back for the promotional video; where one London home has Stan visit to clean carpet and upholstery. Cue lots of Prochem pack shots and the mighty Powermax. Nice job!
“We’re very pleased with that,” says Stan. “It was filmed and edited by professionals and it really shows.”
And it works, too: visitors to the site, many drawn from the company’s social media page reviews, enjoy seeing how a professional cleaner works and are encouraged to use the company for their own homes.
Likewise, the city’s many lettings agencies are attracted to Sky Cleaning’s bright and engaging approach to selling.
Sky Cleaning operates two teams in two VW Transporters. Right now, Stan and his business partner Stan Temelkov are preparing to revise their vehicles’ in advance of the 2020 regulations.
To help improve air quality, an Ultra Low Emission Zone (ULEZ) already operates 24 hours a day, 7 days a week, within the same area of central London as the Congestion Charge.
Most vehicles, including cars and vans, need to meet the ULEZ emissions standards or their drivers must pay a daily charge to drive within the zone. Tougher standards are on the way in late 2020.
Sky Cleaning is electing to meet the emissions.
Watch this space to see how they do it (and enjoy the film) : www.skycleaninglondon.co.uk
More on meeting the ULEZ emissions standards at tfl.gov.uk/modes/driving/ultra-low-emission-zone
Fog lifts smoke and fire damage
Cleaning up after fire and smoke damage? Not got the foggiest what to do? Read on …!
Ask anyone who’s ever had to handle fire damage and restoration and they’ll tell you about ‘the enemy’ that’s carbon and soot build-up.
Smoke and carbons are invasive; they find their way into hard-to-reach areas such as suspended ceilings, into walls, and contaminate carpets and fabrics leaving a carbon build-up that wiping merely smears.
One useful piece of kit for resolving this is Prochem’s Tri-Jet Fogger.
It’s non-thermal so you can break it out and crack on with the job right away, and can be used for high level cleaning and fumigation after fire damage.
It also has applications for anti-bacterial disinfecting and virus control in healthcare markets as well as for odour control in multiple environments.
Constructed of lightweight aluminium, it can discharge or spray a droplet solution of between 15 microns (low) or 30 microns (large) up to 30ft away via its three counter-rotating spray nozzles.
The resulting mist penetrates those inaccessible areas and starts to decontaminate the carbon build-up, without having to get the ladders out. Robust and versatile, the Fogger’s tri-jet head perches on a 4 ltr tank, providing ample solution capacity while being easily portable.
That’s the technology out of the way – what about the solution that goes in it?
Well, first off, used with correctly-diluted Prochem A222 Smoke & Odour Neutraliser, this unit can be used on most wet-cleanable surfaces, carpets and fabrics, spraying out an adjustable neutralising mist to tackle smoke, tobacco and fire residue odours as well as most other lingering odours.
If fogging after a fire, mix 100ml of A222 per litre of fresh water and spray using the Tri-Jet Fogger for 15 minutes over an area of 10m2. Ensure that the room is sealed during the process and for a further 24 hours afterwards and then open all possible windows and allow fresh air to ventilate the affected environment.
Smoke & Odour Neutraliser can also be used in a general cleaning application mode, when either wiping lightly-contaminated surfaces or added to the extraction tank in your machine to deal with carbon and smoky odours.
Another fantastic solution for treating smoke staining and odour to upholstery is A217 Ultrapac Renovate. Check out this recent treatment to smoke-damaged upholstery using it…
Ultrapac Renovate has been formulated to remove smoke, soot, nicotine stains, grease, carbons and ingrained soils.
Used widely for heavy duty industrial cleaning of floors, walls, carpets, hard and porous surfaces as well as for fire damage restoration, it is the perfect solution to have to hand in the cleaning up of smoke and nicotine damaged surfaces.
To use, start by diluting at a rate of between 1:20 and 1:100 (depending on level of soiling). Mix with 4 parts water when using a pressure washer.
Apply to the surface using a sponge, sprayer or floor machine, allow up to five minutes contact time and rinse thoroughly. Finally, extraction rinse fabric and carpets using B109 Fibre & Fabric Rinse.
Fire damage restoration work can be lucrative: have the right solutions to hand and benefit from this valuable area of professional cleaning.
2020 – start the decade knowing more!
The dawn of a new decade is as good a moment as any to consider whether you have the latest knowledge and skills. Solutions and techniques change – making a refresher a valuable start to the year.
Professional cleaners can access premium training in 2020 from Prochem Europe – the UK’s principal commercial provider.
Dedicated course topics span carpets, hard floor and upholstery cleaning as well as stain removal. So what do you get?
For carpet cleaners, contract cleaners or public sector operatives, the 1-Day Carpet Cleaning Course is ideal for improving skills and revealing more about products and methods.
The 1-Day Upholstery Course and the 1-Day Hard Floor Maintenance Course are for cleaners looking to expand their service offer beyond just carpet cleaning.
And for those new to carpet cleaning, take the 2-Day Carpet Cleaning Course and pick up advice on starting up your cleaning business, hands-on practice identifying fibres and carrying out a professional survey. Time poor? There’s an option to take the second day at a later date, if you prefer.
All of these courses provide the opportunity to try out different machines and experienced trainers are available to answer your questions. Training courses are also backed up by a technical help-line and even personal advice via email.
Find Prochem Europe 2020 training dates and details via this link
…while Tom’s back to training after 30 years
1989: Sky TV has started broadcasting, unemployment is at a nine-year low, Ford takes over Jaguar, the M42 is completed. And 30-year old cleaner Tom Sultana is taking himself on a training course with Prochem.
“I went on a two-day course to study carpet and upholstery training,” recalls Tom. It turned out to be money well spent as he has steadily built himself a successful and well established business in Bromley-based All Gleaming Clean.
Now he’s back at the Prochem training academy on another upholstery course. Has much changed? “The biggest change is the emphasis on health and safety'” says Tom. “Of course we know more than we did about the subject today.”
And did he actually learn anything new? “Yes, and I’ll be honest and say I didn’t think I would!” laughs Tom. “I run my two-year old Everest seven days a week, with my son Ben with me now, and being on the job itself has in my view been the best way to learn the trade.
“But I’m pleased to say there is still more to learn about processes and of course there are many new solutions to be tried and tested.”
Prochem – revived 45!
Forty-five years since it started supplying carpet and upholstery cleaning solutions and equipment, Prochem Europe stands as one of the UK market’s principal innovators.
2019 has seen that ethos take material form in the company’s new research and development laboratory facilities at Chessington along with recent investment in new labeling and filling technology.
Alan Tilley managing director says: “The extra lab space means we can work on a growing number of new formulations and increase our work on environmental and sustainable product development.”
The new Prochem lab at Chessington
Scroll back to 1974 and the carpet and upholstery cleaning industry as we know it was just getting off the ground: “there was no such thing as soil extractors, and there was very little training available” says Alan.
Prochem founder, and Alan’s father, Ron spotted an opportunity and started providing courses on carpet, upholstery and floor cleaning in London. This swiftly led to sales of hot water extraction equipment from the USA where the innovation had started.
The Steemeasy machine was one of the first to appear on the UK market and later that year the “Prochem” brand name was trademarked by the company.
Prochem started to develop formulations and cleaning systems to suit the UK carpet cleaning market, including the now widely-used concept of pre-spraying and acidic rinsing. At the same time, the company developed specialised training courses for the new extraction process while advising cleaners how to improve on the traditional “shampoo” methods still being used.
Ron’s enterprise went from strength to strength to become one of the most recognised names for carpet and fabric maintenance products and training.
In 1978, Prochem introduced a new generation of engine-driven truck mounted carpet cleaning machines to the UK market and by 1980 was manufacturing cleaning solutions at premises in Kingston upon Thames.
Prochem Europe HQ in Chessington
In 1994, the fast-expanding business re-located to much larger premises in Chessington with capacity for expanding manufacture, storage, laboratory product development and equipment sales and service.
The new building also provided for a dedicated two-storey training facility; thousands of trainees have subsequently attended Prochem courses there.
Today, Prochem Europe has grown into one of Britain’s foremost providers of specialist cleaning technology and solutions as well as being one of the largest commercial providers of training to the cleaning industry.
In 2012, the company was granted a Royal Warrant of Appointment to Her Majesty The Queen for the supply of carpet cleaning products.
In 2015, the company was accredited to British Standard EN ISO 14001: important to the business as well as reassuring for customers to know they are procuring cleaning solutions from a manufacturer with certified levels of environmental awareness.
Alan Tilley concludes, “I do feel our continued focus on the values that resulted in the Award measure why we are successful: developing safe and effective products for cleaning and maintenance for now and the future.”
A Cleaner’s Tale
Blood stains prove no challenge for Jason Bingham of Platinum Clean …
“A home owner called me one morning recently about a stain problem on a mattress. She emailed me over some pictures and I found I was looking at blood staining to a mattress as well as the carpet beneath the bed.
“I’ve been in cleaning for a year now ever since an accident at work put paid to plastering as a trade and my mind raced with solutions to this customer’s dilemma.
“Platinum is run by my wife Cally and her cousin. We’re in Spalding, Lincolnshire. It started in September last year and there are of six of us in total now – it’s a great business.
“Fortunately, the first thing I learned in building was to have the right tools to hand and I apply that ethos to my work as a cleaner. We bought a Prochem Galaxy extractor recently from our local distributor Hugh Crane in Acle, Norfolk, and that’s a fabulous machine. The guys at Hugh Crane showed us how to use it and what to use with it.
“So, I went on site the morning after the staining – a torn varicose vein – with B144 Stain Pro and B109 Fibre & Fabric Rinse. I sprayed the former to the affected areas and then did a few passes with an extractor hand tool with the rinse: total success!
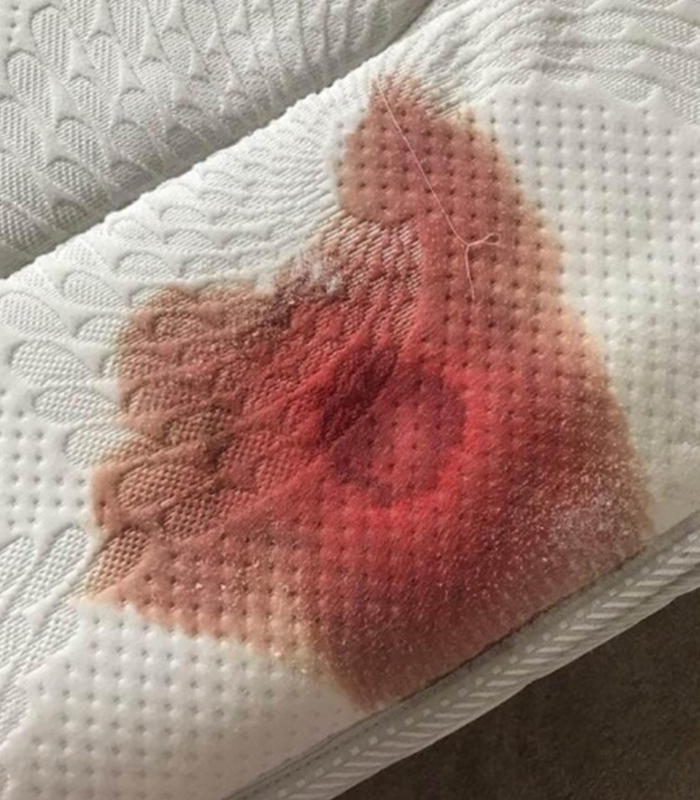

Before and after…
“We’ve recently started using Lemon Refresh and Multi Pro with some great results, too.”
Winter Tips – nipping the freeze in the bud
Winter’s on its way. It may relatively mild now but an extended-range forecast for central England has been predicted seeing temperatures plunge in January and February, trumping even 2018’s ‘Beast from the East’, which caused widespread disruption.
So, it’s worth bearing in mind that machines and accessories as well as chemicals left in un-garaged vans and out-buildings can be vulnerable to extreme cold.
In fact, given how pumps and brass unions are so prone to freezing and fracture during the cold weather, it is sound practice to bring your equipment under cover wherever possible.
The smallest amount of water can expand under freezing conditions and crack equipment, the consequential damage necessitating expensive repairs and equipment down time.
You can prevent water freezing inside your machine by adding an anti-freeze solution; just don’t forget to flush it out before you clean carpet or upholstery!
Truck mount units
To avoid a blown heat exchanger, try adding anti-freeze to your truck mount unit. As with a portable, you would still need to flush the system before using the unit to clean.
Wands and hand tools are the most common items damaged by cold conditions. They are often left in vans their valves and pipework have very small diameter bores, so even the smallest amount of water will cause a lot of damage. Take them indoors, if possible.
Cleaning solutions
And don’t forget, many chemical products are also sensitive to extremes of temperature.
Particular care should be taken to ensure that chemicals are not allowed to freeze in the back of your van or lock-up.
Freeze/thawing of chemical products can affect their stability and performance. At the end of the working day, store your chemicals indoors in a cool, dry location at a temperature above 5C, but below 30C.
You don’t want to find the following morning that your carpet cleaning solution is now an icy solid!
Anti-freeze protection for truckmounted machines: our guide
Just as you use antifreeze to keep your van running through the winter, so you can protect truck-mounted extractors from freezing up.
To introduce the antifreeze, start up the truck-mount with the auxiliary pump turned off.
Now switch on the solution pump and then attach the open-ended hose and bleed off half of the water box volume. Next, disconnect the open ended hose and add 2 litres of antifreeze to the water box.
Run the engine for 10 minutes to allow the antifreeze solution to circulate. Finally, switch off the solution pump and turn off the unit.
To remove anti-freeze from your truck mount, start up the machine ensuring the auxiliary pump is turned off.
Switch on the solution pump, attach the open-ended hose and bleed off the system until the water box is empty (catch the antifreeze solution for re-use).
Now, switch on the auxiliary pump and flush the system until no antifreeze is present. Finally, switch off the solution pump, remove open ended hose and turn off the unit.
Job done!
(You’re receiving our monthly news update from us because you are either a user or distributor of Prochem products. We aim to keep you appraised about our technology and solutions this way but if you don’t wish to continue receiving our news, you can unsubscribe here.)