In this issue:
Missed the last issue? You can read it in full here…
London calling! Prochem makes a must-see of the Cleaning Show!
Look out for Prochem Europe this March (2017) at the UK industry’s leading event, The Cleaning Show.
The event is a must-see for anyone serious about the cleaning business. Held at London’s Excel venue 14th-16th March, it draws thousands of leading suppliers, wholesalers, technologists, cleaners and all types of customers and specifiers to its compelling blend of showcases, seminars and trade stands.
On Stand F10, Prochem Europe will be introducing visitors to its very latest product programmes spanning chemicals, accessories and machines of all sizes and types.
Amongst a strong chemical turnout will be, for the first time on show, versatile B106 Extraclean solution. Ideal for carpet, rug and upholstery extraction cleaning, its formula includes an odour neutraliser and it also benefits from having a pleasing new Lemon Breeze fragrance to wow the building occupier.
Prochem is also bringing along a wide range of cleaning technology. Ever-popular portables include the new Endeavor 500, the Bravo, Fivestar, Polaris 500 and 800, Steempro Powerplus and Powermax.
And you cannot miss the stand: the truck mount display includes a Sapphire Scientific 370SS unit and a Blazer GT housed in a big white Prochem van!
All this, and a full range of Birchmeier sprayers, selection of hand tools and related accessories.
And as ever, Prochem experts will be on hand to help solve any questions and queries.
Training drives expansion at Avica UK
Training is fundamental to what’s driving Avica UK forwards – and Prochem Europe is playing a key role in helping the cleaning and hygiene products distributor boost year-on-year sales.
It’s all about growth at Avica. The company finished 2016 with year-on-year sales up by over 30%.
It’s Tunbridge Wells office and warehouse has just been relocated to larger premises, following similar expansion of its branch in Northampton in 2015 and, last year, the company’s opening head office premises in Watford.
Established over 20 years, Avica supplies cleaning contractors, care groups and facility management companies in the UK. A member of Jangro, it uses group buying power to offer a competitive pricing proposition across a wide range of products.
These are complemented by customer training, available on-site or at its own training centre, based on the Jangro Learning Management System.
Sales staff also benefit from product training. Prochem distributor training has been enabling better understanding of the company’s machines and solutions, as Avica general manager Trish Kerfoot relates:
“We aim to ensure that our sales people have a thorough knowledge of what they are selling and the benefits products bring to customers.
“We have been dealing with Prochem for fifteen years now and sales manager Phil Jones has provided us with two training sessions in the past year that have proved invaluable in helping us shape the right solution for specific user needs.
Says Trish: “The first session included a group discussion about chemicals and a demonstration of the Fivestar upright self-contained carpet, floor and upholstery extraction machine.
“Phil then came back to do a practical demonstration of cleaning using a Steempro, a Polaris and a TM4.
“Around 20 staff have now attended these sessions and the feedback has been uniformly positive.”
Says Avica UK managing director Jeremy Thorn: “there’s a clear connection between product training and sales.
“As a professional training provider itself, Prochem is particularly well placed to help its distributors win machine and solution business.
Jeremy confirms: “We’ve experienced significant sales growth across all three of our branches in the past year, feeding demand for more products available for next day delivery.
“We remain totally focused on exceeding our customers’ expectations with the aim to launch into new territories with the same high quality service and product range.”
Extraclean stands up for diversity
A carpet, rug and upholstery extraction solution that cleans, neutralizes odours and reduces re-soiling is being launched this year by Prochem Europe at March’s Cleaning Show at ExCel, London.
In a crowded solutions market, B106 Extraclean stands out for the diversity of its performance characteristics coupled to its sheer effectiveness in the field.
A Woolsafe-approved maintenance product for wool carpets and rugs, this advanced formulation extraction detergent utilises a micro-encapsulation anti-resoil formula for effective extraction cleaning of all types of carpet fibres, rugs and upholstery fabrics, leaving a pleasant residual Lemon Breeze fragrance with an odour neutraliser.
Read all about it!
B106 Extraclean is one of the latest range innovations to be found in Prochem Europe’s 2017 Catalogue.
Over 40 pages, this quality A4 publication summarises and illustrates all of the company’s chemicals, portable and truck mounted cleaning machines and accessories with full pricing details for simple, easy to use procurement either from its extensive distributor network or its e-commerce facility at prochem.co.uk
Also included in the new catalogue is a training section detailing the latest programme of comprehensive courses spanning carpet, upholstery and hard floor cleaning and stain removal available at the company’s dedicated academy in Chessington, Surrey throughout 2017.
The new catalogue can be ordered now by calling 020 8974 1515 and is downloadable here
Gum no sticky problem for Citrus Gel
Loved the world over, chewing gum is not so popular when it comes to cleaning up.
According to the Local Government Association, while the average piece of gum costs about 3p to buy, it conversely costs around £1.50 to clean up.
The problem of discarded gum is most acute in towns and city centres with London’s Westminster Council suggesting almost three million pieces being dropped on West End streets, annually.
The issue has not been helped by the restrictions being placed on the sale of aerosol products containing hydrofluorocarbons (HFCs), to be banned in aerosols from 2018 due to their contribution to global warming.
But while Prochem Europe has consequently discontinued its G240 Chewing Gum Remover aerosol product, equally efficient alternatives from the company’s range can be used for removing chewing gum.
One immediate standout solution is E840 Citrus Gel, a citrus solvent and detergent based liquid gel spot remover for oil, grease, tar, gum and other oily spots and sticky substances on carpet and fabrics.
Citrus Gel can be used safely on many spots and stains and is formulated to work on the fibre surface, avoiding problems to latex and bitumen backings which commonly occur with other citrus based solvents.
With a pH 5, it comes in 1L containers and ready-to-use on Mr Wrigley’s sticky confection!
Expertise and discretion first for CPS
When it comes to marketing, ‘less is more’ at Phil Dowsett’s Carpet Preservation Services Ltd (CPS) business in Danbury, Essex.
“It’s not that I don’t believe in marketing, on the contrary, I’m just not quite so obsessed with advertising, branding and so on,” says Phil. “I believe that we are only as good as our last job and sticking with that ethos has been good for this business.”
CPS has been cleaning London’s finest hotels for over 30 years. “Our customers look for expertise and discretion over frills,” says Phil. “Our vehicles are not sign-written as around twenty percent of our business is sub-contracted so it’s best they are not.
“We handle quite a lot of demanding jobs working high quality projects and some businesses can be put off by their complexity.”
CPS employs a small team of three, along with Phil and his assistant. One van works nights in the West End and City while the other journeys in and out of the capital on day jobs.
“London is booming still, but to make it there you have to deliver,” says Phil.
“Regular and effective training is absolutely essential to understand differing fibres and their cleaning needs; to determine how best and safely to remove a stain and with what treatment; to take on board management disciplines like proper job scheduling to ensure you make the most of valuable time on site.
And what about pricing? “We price competitively – there are cheaper alternatives out there but the canny customer comes back because we know what we are doing.” They understand price isn’t everything.
Phil uses Prochem Europe training: “ we attend the Prochem courses: carpets, rugs, upholstery and stain removal and what we do like is the help and support we receive from Prochem when we have a tricky job to take on. “I am convinced that going on these courses gives the team the expertise and confidence to go out and get the job done, no matter how challenging. The discerning customer recognises this, and comes back.”
Prochem solutions feature extensively in the vans’ racking. “Fibresafe Gold is a fabulous extraction detergent and B137 Fine Fabric Solvent Cleaner is another regular in our armour,” says Phil.
He’s been buying Prochem products for years now. “Prochem is a business based on our shared values of quality and product integrity.
“They have consistently innovated over the years to bring better and better solutions to market. There are cheaper cleaning products, but not with those performance qualities. And performance is what has made our business.”
Phil adds he is nearing retirement and is looking to move on and perhaps involve another company in the business leading ultimately to a take over, a great opportunity for anyone in the business of carpet, upholstery and curtain cleaning.
Find out more: www.cpsweb.co.uk
In the news? You can be!
News is everywhere around us, these days. So, where do you go to find out about professional cleaning?
Straight to a search engine, but after that? And possibly to cleaning news media sites, like C&M’s and the Cleanzine.
If so, here’s another to add: www.prochemcleaningnews.com
It’s been hosting the latest news and views not only of Prochem but our distributors, the professionals who source Prochem machines and solutions, and their customers: from home-owners and housekeepers to managers and facility managers.
Prochem’s very own, dedicated news site is not ‘new’ so much as refreshed and we hope you enjoy the more ‘content-rich’ experience it now offers.
You will find our latest news releases covering product innovation and our participation at key industry events throughout the year.
Subscribe to the popular Prochem Europe e-zine – it’s the best quick-guide to our (and your) world you can find.
Delve into the past: you can find the entire back copy archive of our magazine ‘Cleaning Specialist’ on the site. Hours of reading fun!
And don’t forget: this news site is meant to be about you, too. If you sell or use Prochem products and would like to be featured on our site in our news media, just get in touch!
Innovative NHS project puts cleaners back into the community
2017: the Clean & Care team
‘Highly Commended’ in the 2016 BIFM British Institute of Facilities Management Awards, South London & Maudsley NHS Trust’s innovative Clean & Care project has gone from strength to strength – and Prochem Europe is cited as key contributor to its success.
Established at London’s Tooting Bec Hospital in 1993, the project, now run by Lambeth Vocation Services, was one of the first in the UK to offer paid work and training to adults in contact with mental health services.
Back then, patients on therapeutic schemes reported their work as menial and unrewarding. A group was set up to discuss opportunities for employment and it was agreed with patients that carpet cleaning would meet the criteria for ethical and meaningful paid work.
Originally named Home Cleaning Services, the team received national recognition, winning an equality award and Beacon status from the Department of Health.
In 2003, the project received a grant from Guys and St Thomas’s Charity which enabled the purchase of more equipment and funding for a full time Project Co-ordinator in Kevin Poulton.
“From the very start, the project had bought Prochem machines and chemicals,” he says. “The machines have proven reliable and long-lasting and as with the chemicals are easy to use and highly effective.”
In 2007, the project became part of South London and Maudsley NHS Foundation Trust Vocational Services and began to receive core funding from the NHS as health professionals and service users alike recognized that meaningful work, increased income and a renewed sense of purpose were important to improved mental health and well being.
“Being awarded a £368K contract from Lambeth Council to clean carpets and floors in Lambeth libraries enabled the project to grow significantly and take the work to an industrial scale,” says Kevin, “We have now diversified from carpet cleaning into more broadly based office cleaning with a new name Clean & Care and, recently, a brand new business web site too.”
More recently, the project has also invested in training, enabling team members to attend courses at Prochem’s training centre in Chessington. Kevin reports the training the cleaners receive as ‘substantially improving’ the results they achieve.
1993: The first Tooting Bec team – going Prochem!
“Training has been core to developing our people and creating a commercial enterprise that offers professional carpet, floor and upholstery cleaning at competitive rates in offices, homes and hospitals while also enabling hundreds of people who have worked for it to learn work skills, gain self-confidence and achieve vocational goals,” he relates.
“Customers have been very impressed and our cleaners pick up the skills to help them go on to work in full employment or education under their own initiative, as indeed many now do.”
Clean & Care use Prochem Steempro extractors on carpets, upholstery and hard floors as well some hard surfaces and favour a complement of chemicals including Multi Pro, the Natural range, Fibre & Fabric Rinse, Prespray Gold and Neutra-Soft.
Says Kevin: “These work well for us and as with all things Prochem, are professional and reliable tools for the job.”
Find out more: www.cleanandcare.org.uk
How To Clean … leather upholstery
Leather is a wonderful and natural material that’s hard wearing and luxurious into the bargain. But improper cleaning can result in costly damage.
So, how to ensure there can be no ‘hiding’ (sorry!) place for soiling in leather upholstery?
The answer lies in a double-whammy of Prochem Europe cleaning solutions.
First out of the traps is E672 Leather Cleaner, an upholstery cleaner and conditioner containing speciality surfactants and neatsfoot oil.
It is a mildly acidic cleaner, specially formulated to clean pigmented smooth hides (it’s important to note that it is not recommended on Aniline hides) and has a pleasant light lemon fragrance.
Here’s how to get the best out of it:
1. First of all, test carefully for colour transfer on the leather upholstery
2. Work the cleaner into the hide using circular motions
3. In areas of heavy soiling, it is worthwhile using a Tampico brush to loosen soil
4. Now, prepare a solution of Prochem B109 Fibre & Fabric Rinse diluted at 50ml per litre of water. Immerse a clean cotton towel in the solution and then ring it out until damp and go over the area just cleaned to remove soil and cleaner.
Now, we can move on to the best finishing treatment you can have for leather upholstery and that’s E675 Leather Conditioner.
This finishing treatment and conditioner replaces natural oils removed through cleaning. It also works well in general use on smooth pigmented leather, restoring suppleness and helping protect against cracking & stains.
The key point with this non-greasy product is to use it sparingly (less is better!)
1. Firstly, (as ever) test for colour transfer
2. Now, spread E675 evenly to the hide using a slightly damp white towel.
3. Leave the solution to dry for five minutes and then buff it using a clean dry white towel. Job done!
Finally, here’s a useful tip: price this conditioner into your job when you quote. They will be delighted with the ‘like-new’ look of their leather upholstery, which hopefully will reward you with more work in the future.
“Training changes everything” says Moston of Manchester
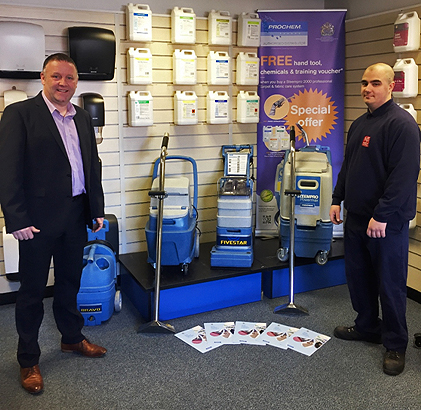
Darren Ford (l) with David Young
One Prochem distributor looking forward to the company’s regional training course in Birmingham is Darren Ford, Director at Manchester’s Moston Janitorial Supplies.
Darren has attended these courses before and is another fervent champion of Prochem training.
“Training changes everything,” he tells us. “My role is essentially business development so I have to know what I’m talking about when I’m recommending solutions to customers.
“Training means understanding and that’s really confidence-boosting. I have been on a number of Prochem courses and am looking forward to March’s session at Birmingham City FC.”
He’s not alone at Moston – office manager Joanne Newell and trade counter operative David Young attended last October’s regional training course at FC United of Manchester’s football ground.
“I really enjoyed the whole day,” says Joanne. “Phil Jones was brilliant at getting technical points across straightforwardly and was so helpful. Like Darren, my role is selling so I need to be up-to-speed with what works for different situations.
“With Prochem products and machines being prominent in our trade counter area, the next enquiry we had both David and myself were able to advise accordingly, with the customer buying a Steempro Powermax and stair tool together with the right chemicals to get started, so I would definitely recommend the training course and I am looking forward to the next refresher course.”
Darren’s parents started this family business back in 1976 and it has steadily grown into a principal supplier of quality cleaning chemicals, paper products, vacuum cleaners, sweepers and scrubber dryer machines to a diverse customer base spanning industry, healthcare, schools, and contract cleaners operating in and around the city and outlying area.
Moston Janitorial Supplies sells Prochem Steempro machines regularly, along with what Darren sees as the essential package to ‘get you on the road’, including Extraction Plus, Multi Pro, Odour Fresh, Fibre & Fabric Rinse.
“That’s the smart solution to getting on in cleaning,” he says. “The right tools and, with some training, the right knowledge!”
Find out more: www.mostonjanitorial.co.uk
Label colours tell the scale tale – part 3
In previous issues, we have looked at the basic elements of the pH scale and established how there truly is ‘strength in numbers’. This month, we round off the series with cleaning solution recommendations that enhance the overall result.
To recap, this is all about the pH measurement scale involving water-based liquids, and the Pantone reference colour codes that Prochem has adopted for chemical labels to help users identify its products.
So: as we now know, most soil is acidic and therefore alkaline products aid in Its removal.
This releases the soils “magnetic” attraction to the fibre and turns it in to water-rinseable residues. This method, if you remember was called saponification. On a soiled carpet, such as in a high traffic lane, an application of a pre-spray, pre-treatment or traffic lane cleaner will help to create saponification.
It will loosen the soils and help the machine work far more efficiently, giving a deeper clean. In fact, the pre-spray should be deemed to be the best cleaning process for heavy soil – the machine just has to rinse away the pre-treated, solubalised soils.
Now it would be reasonable to ask ‘which pre-spray?’
Depending on soil levels, soil type and carpet fibre type, a trained carpet technician should be able to make a correct choice.
For example, in the Prochem range, pre-spray products vary between a mild pH8 (Prespray Gold) and go up to an industrial strength level of pH11 in Trafficlean and Power Burst.
Whichever product is chosen for the individual task, it should be diluted correctly with warm water and sprayed onto the carpet from a height of 8-12” from the surface.
Consider spraying a heavier soiled area slightly slower, allowing more product to make contact with the excessive soils.
Agitation with a suitable carpet pile brush will certainly aid the soil breaking capability of the product and then allow a short dwell time for the pre-spray product to actually do its job and soften the soils. A suitable dwell time could be anything between 2 to 5 to 15 minutes, but always extraction rinse the carpet before the prespray has dried.
There is a very appropriate 4-letter word for this process that is well worth memorising – CHAT.
If you have chemical (C) and you dilute it correctly with warm water (Heat – H), give it suitable agitation (A) and allow time (T) then you have all the ingredients to get excellent results.
Just to remind you, that carpet presprays are alkaline and are not intended to be left in the carpet fibres. They should be rinsed out with a spray extraction carpet machine. So what to put in the machine to aid the rinsing process ?
A trained operator would often use an acidic rinse detergent in the machine, correctly diluted with warm water, such as B109 Fibre & Fabric Rinse. This will aid the release of soils from the carpet as well as balancing the chemical residue in the carpet fibres.
As a guideline, if we have used a prespray of pH8 to pre-treat the soils, the carpet is at that moment left mildly alkaline.
If we then use a carpet detergent (or rinse) of pH4 and rinse the pre-treatment soils and water away, we have neutralised the chemicals and left the carpet roughly pH6.
Let’s think of the pH scale as a see-saw.
By using a pre-spray, we load one side of our see-saw with pH8 (Prespray Gold). Next we rinse the carpet or load the other side with a pH4 (Fibre & Fabric Rinse). Now the see-saw is balanced at roughly pH6.
Now let’s do the calculation in our heads.
Add the pH value of the pre-spray (8) and the pH value of the rinse (4) together, and we have 12.
Divide by two, and that is roughly the finishing figure for the carpet’s chemical level e.g. 6!
Finally, yes, there a few factors that would affect this calculation, but as a rule-of-thumb, it’s a good place to start when it comes to understanding pH scales and making them work for you.
Rogaland boost Endeavor fleet to five
Ship cleaning with Rogaland …
Norwegian cleaning contractor Rogaland Teppe is a fan of the new Prochem Endeavor 500 extractor – the company has recently taken delivery of another two machines to add to a fleet of five 500s as well as its fleet of Prochem Everest and Performer truckmounts.
Rogaland works all over south Norway but its investment in Prochem technology has enabled the company to broaden its range commercially and geographically: when we call general manager Arnt Garpestad, he and his team of seven are in Denmark cleaning cruise ships
“Yes, business is good,” says Arnt. “Our latest Endeavors arrived safely, on time, and working very well.”
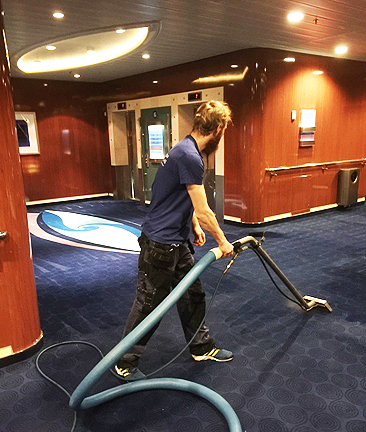
Ship carpet cleaning with Rogaland
Rogaland Carpet and Furniture Cleaning AS is run by Arnt and his wife, Nina. The business was established in 1981 by Nina’s father, and specialises in carpet and upholstery, with offices in Oslo and Stavanger.
Contracts span office buildings, cinemas, ships, hotels, restaurants and private homes with a client list ranging from many of the largest companies in Norway. Rogaland also picks up a substantial amount of sub-contracted work from the region’s principal cleaning companies.
Truck mounts are equally popular with cleaner and clients, Arnt tells us. “These machines are the best on the market, offering tremendous vacuum, water pressure and fast drying times – their overall performance is outstanding,” says Arnt.
“If for some reason, such as poor vehicle access, we cannot use them on site, the Endeavor is the next best solution being portable and very powerful, also.”
The cleaners at Rogaland are equally pleased with Prochem chemicals.
“We buy across the range but if I had a favourite it would Fibresafe Gold – that’s a fantastic product,” says Arnt, and with that, he’s back to a big ship’s carpets.
Find out more: www.rtm.no
2017: get learning earning!
Maybe it’s the time of year (new start, knowledge needs a re-boot) but it’s always busy at Prochem’s Training Academy in the early Spring.
As fast as new course dates are announced, the bookings start coming in – and it’s the same for regional courses both for Prochem and distributors offering training.
People attending Prochem training courses come from all different walks of life and can range from established cleaning professionals to folk entirely new to the business.
There are one and two-day carpet and upholstery course dates to choose from along one-day stain removal sessions.
Newcomers to cleaning should certainly consider attending a two-day course. For the more experienced, a refresher course to nail the essentials of carpet cleaning with a one-day-course would be ideal.
And if you have already completed a Prochem one-day-course, you can attend the second day of a two-day course, enabling you to practise a hands-on survey and learn more about setting up a carpet and upholstery cleaning business. Call Presh Shan on 020 8974 1515 to discuss your options and book your place.
If you are looking for a new career opportunity or want to improve existing knowledge and skills, then Prochem can help you learn everything you need to know about cleaning carpet, upholstery and hard floors.
Prochem Europe is broadening its training offer to professional cleaners in 2017.
The company is staging regional courses for the Midlands and the first of a series of WoolSafe sessions during March, complementing seminars held through the year at its dedicated training academy in Chessington, Surrey.
One-day regional courses staged at Birmingham City Football Club’s ground, St Andrew’s will cover Carpets on Wednesday the 29th and Upholstery on Thursday 30th while the first of Prochem’s WoolSafe training courses is being held on Thursday the 23rd at Chessington where year-round one- and two-day courses covering carpet, hard floor, upholstery cleaning and stain removal are held.
Each course includes face-to-face instruction and step-by-step demonstrations by dedicated Prochem trainers; all delegates take home a comprehensive reference manual to help them put the theory into practice.
More information here
Vanitorials acquire Clean Connections
Two major Prochem Europe south-east distributors are now working as one, redoubling their customer commitments and as members of Jangro, bringing with them the technical support and buying power of the UK’s largest national buying group of janitorial suppliers.
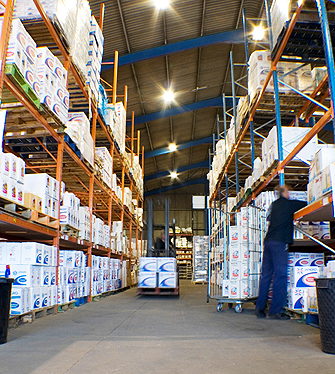
Warehousing at Vanitorials
Benfield-based Vanitorials has acquired Clean Connections of Byfleet.
The move expands their collective stocking capacity and staffing, with extended product ranges, enhanced customer services support and even stronger positioning as a key industry supplier for Essex and the South East.
Warehousing at Vanitorials
Vanitorials operates a 13,000 sq ft distribution centre only 4 miles from Junction 30 of the M25 and the Dartford Crossing along with a 5,500 sq ft office, trade counter, showroom and service centre.
Prochem Europe welcomed the development. “The merger of Clean Connections into the Vanitorials Group increases their joint operational spread gaining added physical presence in Surrey and south London and adds to the levels of customer support they already provide.
“Both share similar values and business ethos and are very valued customers and advocates of Prochem Europe products and services.”
Find out more: www.vanitorials.co.uk
Carpets complicated? It’s no yarn…!
Making carpets is a far more complicated operation than many think. Phil Jones reports in from a trip to the Yorkshire mills – and finds out what a ‘slub’ is!
The bringing together of fibres, tufts or yarns, which are then needle-punched into a netting (often referred to as the primary scrim) and the gluing process of attaching the primary to a secondary backing which gives the carpet stability, is easy to explain.
But we don’t always appreciate all the work that goes on prior to this nor how in-depth it actually is.
Prochem’s sales and training team joined other cleaning product manufacturers, floor care specialists, contract and carpet cleaners to find out more by visiting Yorkshire carpet makers on Woolsafe’s ‘Fleece to Floor Tour’.
An early start at the British Wool Marketing Board reveals how dirty, smelly fleeces from farms around the UK and as far away as New Zealand are sorted according to quality of feel, depth of colour and other factors.
The sorting staff employed at BWMB, have their own hierarchy. A master-sorter requires a minimum of 8 years training to be able to sort and judge the fleece. They merely rub the fleece between their fingers and then decide in a matter of seconds, which market that individual fleece of wool is suitable for – carpets, clothing, etc.
On next to where fleeces are bundled and then sold to the wool buyers at the Wool Marketing Board’s saleroom (like the Stock Exchange in many ways) where we visitors had the chance to “bid” for container-loads of wool (luckily not with our own money!)
We were then able to follow our newly–purchased container load of wool to the next location, Haworth Scouring, where fleeces are washed on an industrial scale.
This process passes the fleeces along a conveyor-belt system consistently being washed with extremely hot water that cleans the wool of all natural debris, such as soil, leaves, twigs, and infestations.
The humidity level and even more, the smell, was quite something and we were happy to get to the far end of the factory and reach the great outdoors. I have the greatest respect for the staff who work in that part of the operation!
Once clean, dry and devoid of waste particles, the wool is re-bundled and sent on to the yarn dyeing facility, on this occasion Lawton Yarns, where my investment was turned into more recognisable fibres from the original fleece.
It starts off by going through a machine that blends either pre-dyed yarn, such as heathers (mixed colour) or stock dyed (plain colour) in with the new wool. At this stage, other ingredients are added if required, such as synthetic fibres – nylon, polyester, acrylic or polypropylene, giving the wool extra strength as bulking fibres.
The carding machine next pulls the fibres to pieces, further blending the added mixture, removing any missed foreign matter, straightening the fibres and producing, out of the far end, a soft, twistless ‘slub’ (what a great word) of mixed fibres.
Spinning takes the slub and helps give the fibres further strength and cohesion. Various amounts of fibres can be added to increase performance – hence 2-ply, 3-ply all the way up to quality 5-ply. It’s like twisting or plating 3 pieces of, say, fuse wire together and finishing up with stronger piece.
The fibres are then made into “hanks” which are large loops of fibres ready for dyeing or colouring. These are immersed into baths of hot water and an acid dye is introduced and the naturally absorbent wool fibre, adopts the new colour.
Once dry, the hanks are back-wound onto huge cones or bobbins, ready for despatch to the carpet manufacturers.
Off we went, across a wet and windy Yorkshire, to GTuft, a tufted carpet manufacturer where we saw how all those processes came together to create what we know and love, a carpet.
The conveyor-belt like machine, fed those fibres from their cones, through thin plastic tubes, to a huge bank of computer controlled needles that punched them through the primary scrim.
The scrim, complete with the fibres then has an adhesive spread over its backside and the secondary backing, such a just/hessian, felt, a synthetic backing etc is added, dried and rolled out. Finally, the carpet is inspected for colour match, any sprouting tufts are trimmed and it is finally rolled onto a huge roll, ready to go to the warehouse and any carpet shop in the country.
In all this was a real education; you get to see the complete process. “Fleece to Floor” lives up to its name.
If you want to learn more about wool fibres, their benefits, how to care for them and more importantly, how to clean them correctly, don’t forget that Prochem is now holding Woolsafe Fibre Care Specialist courses.
Find out more here
Q and A … you ask, we answer!
Q
I’ve got to remove a fruit smoothie later this week. Do I treat it the same as a coffee spill ?
Nenita – Surrey
A
Right there are going to be proteins such as milk or yoghurt as well as colourings to contend with so, yes, you would start off the same way.
An application of Stain Pro and a five-minute dwell time before rinsing out with Fibre & Fabric Rinse or your chosen extraction detergent, depending on the carpet fibre.
Once that has been removed, if you find a light coloured tinge still residing in the pile, then this may be the natural food colourings within the fruits.
So – consider applying E400 Red Rx. This is a food colouring remover. Lift its flip-top lid and feed a small amount onto the colouring, gently work it into the carpet area, and rinse-extract with your machine again.
Please note that this action can be carried out no more than three times, otherwise it may affect the colour of the actual carpet itself. Also, Red Rx should only be used on white, plain, beige and natural coloured carpets.
By the way, an alternative solution is to use Red Rx with hot iron transfer. (If you are not sure about this, visit our Cleaning Technical Help Pages at www.prochem-uk.com for more information).
Q
Can you advise please? I was called in to clean a beige wool carpet laid to a master bedroom in a very nice house, S708 Contract Carpet Prespotter as a pre-treatment and then used S775 Extraction Plus to rinse. The result looked great, but I was back the next day to investigate brown patches in some areas of the carpet. What’s gone wrong here? Is this soil wicking?
Maurice, MG Cleaning Services
A
OK, this is manageable. There’s possibly too much alkalinity on the go here for a wool carpet. Try using B175 Browning Prescription as the spotter and B109 Fibre & Fabric Rinse as the rinsing agent.
This should clear the problem.
Q
I have a Laura Ashley wool rug in grey with beige patterns with orange juice and wine stains to get out. I used B144 Stain Pro to pre-treat the stains and rinse-extracted with S776 Double Clean. It looked fine to start with, but now I’ve got brown patches appearing. What do I do?
Ben, Finest Carpet Cleaning
A
Ben – Stain Pro is absolutely the right chemical to use as it works on anything protein-based like food, drink, blood, faeces and vomit, so that’s a good call. But rinse extracting with S776 Double Clean afterwards meant you left the rug too alkaline for wool fabric.
To rectify this problem, go over again with B175 Browning Prescription as the spotter and B109 Fibre & Fabric Rinse.
(Good news – we heard back from Ben and Maurice and our solutions to their browning problem worked for both of them!)
Q
Hello – I have to clean a grey polypropylene carpet but it has residual curry staining. Can you suggest the best solution?
Eli Patashnik
A
Tricky chaps, curries! We suggest you use B144 Stain Pro as your spotter, work this in with a brush and rinse away with B109 Fibre & Fabric Rinse. Now, apply E400 Red Rx, and using a hot iron and damp towel, you will find the slight tinge left behind should vanish.
(You’re receiving our monthly news update from us because you are either a user or distributor of Prochem products. We aim to keep you appraised about our technology and solutions this way but if you don’t wish to continue receiving our news, you can unsubscribe here, or on your website account settings at www.prochem.co.uk)